As part of the Connected Factory course taught by Lionel Fomperie, VP of Industrial Strategy at Nexans, and Chao Li, Digital Development Engineer at Nexans, A5 students from the Industry 4.0 major visited connected factories.
Nexans, a French multinational in the cable transmission line industry, has been engaged for two years in an extensive industrial digital transformation program with the support of Schneider Electric, a specialist and world leader in digital energy solutions and automation for energy efficiency and sustainability.
This programme will cover more than 40 Nexans sites worldwide and aims to use data from equipment to improve site performance by being more responsive, agile, and flexible
What is a connected factory?
A connected factory uses modern sensors, real-time data analysis, platforms, and robotics.
Connected factories because they use Internet of Things (IoT) technologies to connect their industrial equipment and systems to collect, analyse and use data in real time. This enables better monitoring, more effective preventive maintenance, and optimisation of production processes to improve efficiency, quality, and profitability.
On the other hand, sending data to the cloud or being controlled remotely makes them particularly vulnerable to cyber-attacks.
Industrial cybersecurity is therefore becoming a significant issue. One of the subjects of the training programme at ESILV to raise awareness among future engineers of Industry 4.0.
Use cases such as the Factory Cockpit, digital management routines, and the measurement and monitoring of the industrial performance of each production line allow productivity to be improved by considerably reducing non-value-added tasks for operators.
Through these two visits, organised last January, the A5 students from the Industry 4.0 major, were able to discover the different stages of the electrical cable manufacturing process on a site working traditionally, such as the Nexans site in Paillart, and an area recognised as the international showcase for Schneider’s digital transformation programme, the Schneider site located in Vaudreuil.
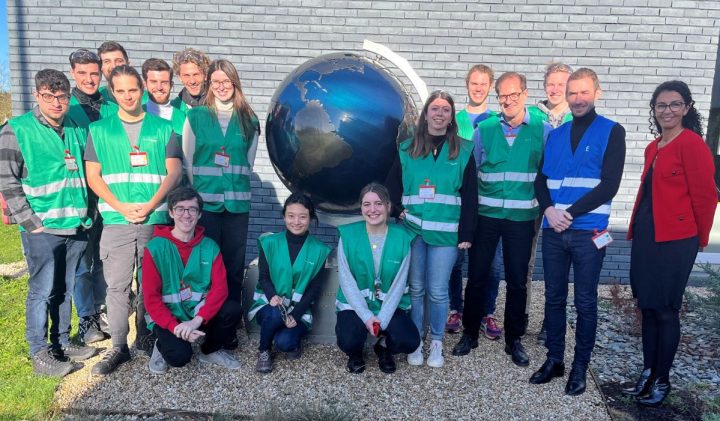
ESILV industry and robotics students during the visit
In this way, the students could visualize the connected factory’s contribution to working methods and responsiveness to everyday activities.
This experience gave the students a more concrete and practical view to follow up on the courses at school and, for some, to become familiar with their future work environment.
Learn more about the engineer’s degree with a major in Industry 4.0